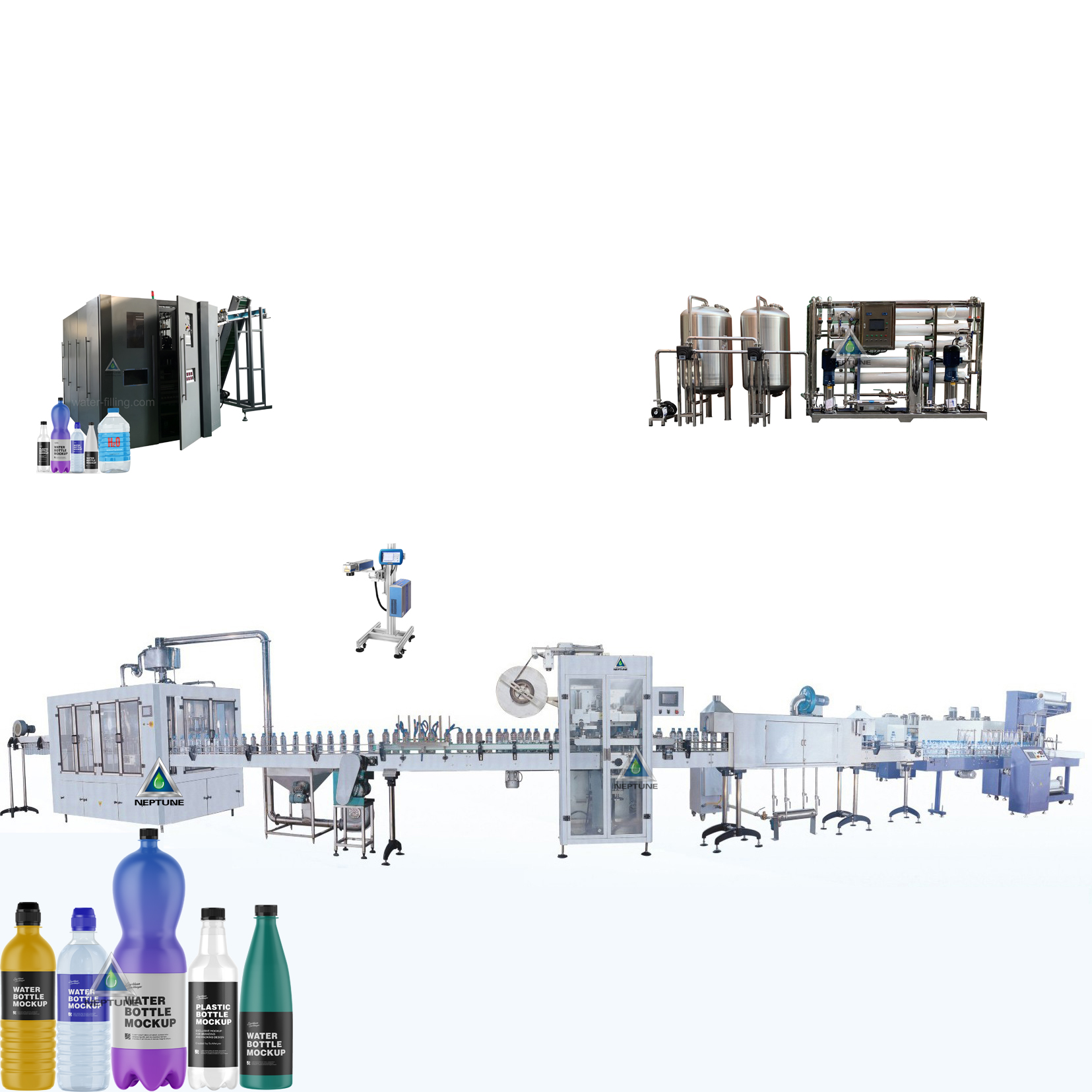
NEP-6000 : WHAT IS THE PRICE OF THIS BOTTLE WATER PRODUCTION LINE:
FOB PRICE $124,200
WHAT THIS PRICE INCLUDED?
Automatic Blow Molding Machine | 1SET | ||
High Pressure Air Compressor Unit | 2SET | ||
Low Pressure Air Compressor | 1SET | ||
HP Air Dryer | 1SET | ||
HP Air filter | 2SET | ||
HP Air Tank | 1SET | ||
Mould Chiller | 1SET | ||
LP air filter | 1SET | ||
Spare parts | 1SET | ||
Air tube | 1SET | ||
Blow Mold (250-1500ml) | 1SET | ||
SUS304 TC-10.0SC PRE-TREATMENT | 1SET | ||
RO-1000(5000LPH) unit [5PSC DOW BW30-400 RO membrane] | 1SET | ||
RS-4 Water Softener | 1SET | ||
5000L1700×3500 SUS304 Water Tank (Thickness 0.8mm) | 1SET | ||
5000L1700×3500 SUS304 Water Tank (Thickness 0.8mm) | 1SET | ||
SOZ-16G Ozone Generator and Mixing System(Air source) | 1SET | ||
120W Ultraviolet sterilization assembly(UV) | 1SET | ||
NF18-18-6 Washing-Filling-Capping (Three-in-One Unit) Machine | 1SET | ||
Air compressor 1/8 | 1SET | ||
Cap elevator SG-1 | 1SET | ||
Convey System US4/18(2M Air conveyor,1psc air blower,4M conveyor,1psc motor) | 1SET | ||
Light check | 1SET | ||
Change bottle use shape mold | 2SET | ||
HP-250 SLEEVE LABELING MACHINE (Come with the steam shrinking tunnel &steam generator&six meters conveyor belt, motor) | 1SET | ||
30W LASER PRINTER | 1SET | ||
AUTOMATIC THERMO SHRINKAGE PACKAGE MACHINE (Come with Automatic film wrappage machine; Bottle convey machine; Thermo shrinkage package machine; Main controlling case; Convey machine rack) | 1SET |
Complete 6000BPH water bottle production line solution from begin to the end do not need any manual. High level automation. Structure compact and easy to operate.
It is the fast-finished production bottled mineral water plant. It included bottle washing, filler water, screw capping, sleeve labeling, wrap package.
Power inquiry | 170kw |
Capacity | 6000 Bottles Per Hour |
Volume of the bottle | 200ml to 2000ml |
Long | 16meter |
Width | 6meter |
Liquid | Mineral Water, Spring Water, Purified Water |
advantage
- High Production Capacity: Produces up to 6000 bottles per hour.
- Fully Automated: Minimizes manual intervention, boosting efficiency.
- Consistent Quality: Ensures uniformity in every bottle produced.
- Integrated System: Streamlines the entire production process.
- Energy Efficiency: Optimizes energy consumption for cost savings.
- Space-saving Design: Compact layout for efficient use of floor space.
- Versatile: Capable of handling various bottle sizes and types.
- Easy Operation: User-friendly interface for simplified control.
Neptune Machinery Company stands as a beacon of innovation and excellence in the realm of water bottling solutions. With a commitment to delivering cutting-edge technology and unparalleled performance, Neptune has established itself as a trusted name in the industry. Among its impressive array of offerings, the 6000 bottles per hour (BPH) fully automatic water production line stands out as a testament to Neptune’s dedication to quality and efficiency.
State-of-the-Art Technology
At the heart of Neptune’s 6000BPH fully automatic water production line lies state-of-the-art technology designed to streamline the bottling process and ensure maximum productivity. Equipped with advanced machinery and precision-engineered components, this production line is engineered to deliver optimal performance with minimal downtime.
High Production Capacity
With a production capacity of 6000 bottles per hour, Neptune’s fully automatic water production line is geared towards meeting the demands of large-scale bottling operations. Whether it’s purified water, mineral water, or flavored beverages, this production line is capable of handling various types of liquids with ease, making it an ideal choice for businesses looking to scale up their operations.
Efficiency and Consistency
Efficiency and consistency are the hallmarks of Neptune’s 6000BPH fully automatic water production line. By automating key processes such as bottle washing, filling, and capping, this production line ensures that each bottle is filled accurately and sealed tightly, eliminating the risk of contamination and ensuring product integrity. With precise control systems and advanced monitoring technology, Neptune’s production line delivers consistent results batch after batch, meeting the highest quality standards.
User-Friendly Design
Neptune understands the importance of ease of use in a production environment, which is why its 6000BPH fully automatic water production line features a user-friendly design that prioritizes simplicity and efficiency. Intuitive controls and a user-friendly interface allow operators to monitor and adjust production parameters with ease, while automated systems streamline workflow and reduce the need for manual intervention. Additionally, the production line is designed for easy maintenance, with accessible components and clear instructions for routine upkeep.
Customization Options
Recognizing that every bottling operation is unique, Neptune offers customization options for its 6000BPH fully automatic water production line to meet the specific needs of each customer. Whether it’s adjusting filling volumes, configuring bottle sizes, or integrating additional features, Neptune works closely with customers to tailor its production line to their exact specifications, ensuring optimal performance and maximum efficiency.
Reliability and Durability
Neptune’s reputation for reliability and durability is reflected in its 6000BPH fully automatic water production line. Built to withstand the rigors of continuous operation, this production line is constructed from high-quality materials and components that are designed to last. Rigorous testing and quality control measures ensure that each production line meets Neptune’s stringent standards for performance and reliability, providing customers with peace of mind and confidence in their investment.
Comprehensive Support
At Neptune, customer satisfaction is paramount, which is why the company offers comprehensive support services to accompany its 6000BPH fully automatic water production line. From initial installation and commissioning to ongoing maintenance and technical support, Neptune’s team of experts is dedicated to ensuring that customers get the most out of their investment. With prompt service and responsive support, Neptune stands by its commitment to excellence and customer success.
Conclusion
Neptune Machinery Company’s 6000BPH fully automatic water production line represents the pinnacle of bottling technology, combining advanced features, unmatched performance, and exceptional reliability. With its high production capacity, efficiency, and user-friendly design, this production line is the ideal choice for businesses looking to elevate their bottling operations to new heights. Backed by Neptune’s reputation for quality and customer support, the 6000BPH fully automatic water production line is a testament to Neptune’s ongoing commitment to innovation and excellence in the industry.
Bottling plant factory layout
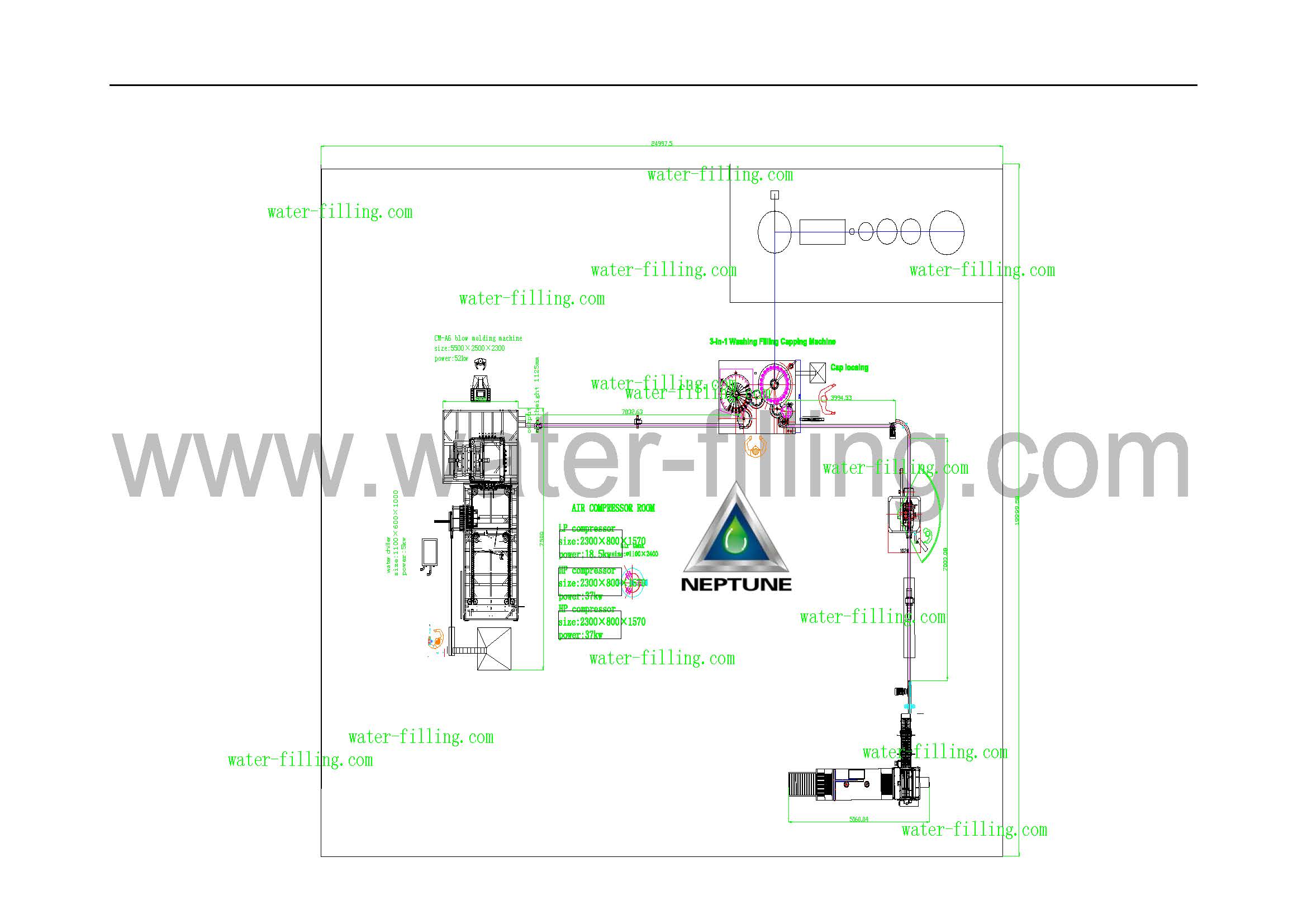
6000BPH water bottle production line is a marvel of efficiency and automation, seamlessly guiding raw materials through various stages to produce high-quality bottled water.
First, a worker loads preforms into the preform loading station. These preforms are then automatically fed into the heating and blowing machine, where they are transformed into plastic bottles through a process of heating and blowing.
Once formed, the empty plastic bottles are conveyed to the water bottling machine, where they undergo a series of steps. The bottles are first rinsed with pure water to ensure cleanliness, then filled with purified water using precision filling technology. After filling, caps are securely placed on the bottles to seal them.
Next, the bottles proceed to the labeling machine, where each one receives a sleeve label. These labels are then heat-shrunk onto the bottles using a shrink tunnel, ensuring a tight and secure fit.
To ensure traceability and quality control, a code printer machine marks each bottle with production date and shelf time information.
Finally, the bottles are transferred to the final wrap package machine, where they are wrapped in film and packaged into bags containing 6 to 24 bottles each. This comprehensive process ensures that every bottle produced meets the highest standards of quality and hygiene.